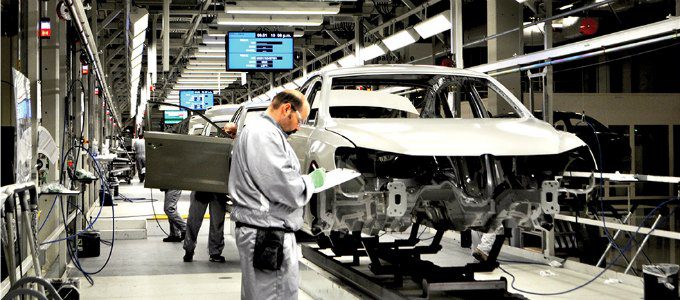
Volkswagen’s Chattanooga, Tennessee, plant faced a dearth of local workers, so the German automaker transplanted a practice from home that is slowly yielding a steady flow of talent.
by Sarah Sipek
June 26, 2015
Amy Meacham spent the past 20 years working in the real estate industry as an administrative assistant. Now she is the future of manufacturing at Volkswagen Group — thanks to a transformation in how the company sources local talent.
In May 2011, the German automotive firm opened its first United States-based plant in Chattanooga, Tennessee, to produce a version of its 2012 Volkswagen Passat NMS, a model targeted to the U.S. market. Given that the bottom had fallen out of the U.S. automotive market in June 2009, when giants General Motors Co. and Chrysler Group filed for bankruptcy, Volkswagen had a vast pool of highly skilled talent from which to recruit.
Source: Photo courtesy of Volkswagon
Instead of exclusively targeting the more than 300,000 experienced automotive laborers who lost their jobs in 2009 alone, according to data from the Economic Cycle Research Institute, Volkswagen went after people like Meacham and Blair Moore, an unskilled assembly line worker with a degree in pre-nursing.
Neither had any prior mechanical knowledge. To Volkswagen, that’s what made them ideal candidates.
“We didn’t want to avoid hiring skilled team members from Detroit and other areas here in the States,” said Sebastian Patta, the executive vice president of human resources at Volkswagen, “but they are not really familiar with our robots, our approaches or even our culture.”
To educate and train new employees on the skills necessary to succeed at Volkswagen, the company turned to a model it has used in Germany for decades: apprenticeships.
About 60 percent of German workers train as apprentices in the automotive manufacturing, IT, banking and hospitality industries. German apprenticeships are based on the idea of “dual-training,” according to the Federal Institute of Vocational Training. Trainees typically split their days between classroom instruction at a vocational school and on-the-job time at a company.
The theory apprentices learn in class is reinforced by the practice at work. Apprentices also learn work habits and responsibility as well as absorb the culture of the company. Trainees are paid for their time, including in class. The arrangement lasts for two to four years, depending on the sector. Both employer and employee anticipate it will lead to a permanent job.
The arrangement is contrary to what’s common in the U.S., where less than 5 percent of high school graduates train as apprentices and the majority of those who do go into the trades, according to the U.S. Bureau of Labor Statistics.
This made introducing the concept and recruiting participants for Volkswagen’s Chattanooga plant difficult.
“There was some hesitation,” Patta said. “People didn’t understand why they had to spend 3 ½ years of their lives training to be an employee at Volkswagen later on. They didn’t understand the approach, and it was a challenge for us to find people at first.”
But Volkswagen stayed with it. The company partnered with Chattanooga State Community College to develop its own dual-education system that combined classroom learning at the college with hands-on training at Volkswagen’s plant to provide apprentices with both a certification as a skilled team member and an associate’s degree of applied science.
‘We’re talking about lifelong learning. It’s not like you learn something for three years, and then you’re done for the future. It’s a permanent learning situation we offer here at the plant.’
—Sebastian Patta, executive vice president of human resources, Volkswagen Group
Four years later, Volkswagen has graduated 25 people from its apprenticeship program. Still, while the model is successfully established in Germany, company executives say they must continue to adjust it to continue to attract and retain local talent unfamiliar with this way of job training. The ultimate goal is to create an employee who is ready to learn and grow within the company for years to come.
“We’re talking about lifelong learning,” Patta said. “It’s not like you learn something for three years, and then you’re done for the future. It’s a permanent learning situation we offer here at the plant.”
Building the Modern-Day Apprenticeship
Before Volkswagen could even begin the process of persuading the U.S. workforce that its apprenticeship program is worth the time, the company had to find a partner school with which to build a program that would meet the standards upheld on its German campuses.
According to Catharina Mette, Volkswagen’s head of communications at its Chattanooga plant, any school that the company partnered with needed to meet the standards set forth by the German-American Chamber of Commerce, formally known as the Deutscher Industrie-und-Handelskammertag. This governing body is in charge of assuring the content of the courses offered in the U.S. matches that of the apprentice programs offered in Germany.
In addition to evening the playing field, this standardization means that successfully completing the apprenticeship qualifies an employee to work at any Volkswagen plant in the world.

Source: Photo courtesy of Volkswagon
“Everyone has to pass the same test,” Patta said. “When you pass your test successfully, you will get a certificate that will allow you to work in Germany as a skilled team member, which gives you a lot more opportunities.”
Ralph Gwaltney, an automation mechatronics professor at Chattanooga State, said Volkswagen chose the school in part because of its past corporate development partnership with the Tennessee Valley Authority, a federally owned utility. He said Chattanooga State’s ability to help students meet corporate standards made it an ideal partner organization.
Source: Photo courtesy of Volkswagon
The program itself is especially designed for skilled team members. Unskilled laborers can be hired without completing an apprenticeship, according to Mette. It lasts nine semesters and is divided between 30 percent classroom training and 70 percent hands-on training.
Additionally, the academy where students participate in classroom training is located at the plant. Hands-on training occurs at a miniature plant adjacent to the actual factory, and is equipped with robots, paint guns and cars for students to train on.
Patta said time spent working in the mock plant is vital to future success at the company.
“Hands-on training means that students have the same environment as they would in our actual factory,” Patta said. “After three years in the program, students will be familiar with the culture, environment and procedures in our plants. That way when they enter the actual facility, they are not completely ready, but they are ready to learn and grow within Volkswagen.”
Apprentices can choose between one of two tracks: car mechatronics and automation mechatronics. Car mechatronics programs provide training in areas related to car maintenance, including manufacturing, welding, automotive technology and diagnostics, Patta said. Those specializing in automation mechatronics will learn to maintain the infrastructure of the plant, including the use and upkeep of Volkswagen’s robots.
But it’s not all nuts and bolts. Because students also receive an associate’s degree of applied sciences upon completing the apprenticeship, they’re responsible for meeting Chattanooga State’s scholastic standards as well.
“In addition to courses in machining and electricity, students are also responsible for satisfying requirements in math, science, arts and humanities courses,” Gwaltney said.
To ensure cohesion between the college and the company, a system for direct communication has been established between academic department managers and the direct supervisors that are responsible for the students when they are on on-the-job training. Such communication has helped students satisfy dual-requirements so they aren’t wasting their time with unnecessary courses.
For example, at Volkswagen’s request, Chattanooga State took out a technical communications class and instead offered students a German language class.
Albert Graser, assistant manager with the mechatronics program on the Volkswagen side, said these classes help build loyalty and excitement for working at a German company. “The interest from our students is very high,” Graser said. “If they are going to have to sit in that type of class, it might as well help build enthusiasm for German culture and Volkswagen.”
Source: Photo courtesy of Volkswagon
Revving Up Interest
Despite creating a comprehensive program, Volkswagen initially had a hard time cultivating interest in it because of a lack of cultural recognition for the recruiting practice. As a result, in the beginning Volkswagen’s strategy was to visit surrounding churches to appeal to the locals.
Applicants were invited for a hands-on test at the plant’s facility to help determine if they had the problem-solving skills necessary to excel. These efforts resulted in a candidate pool composed mainly of Chattanooga residents that weren’t particularly successful.
U.S. Expands Apprenticeship Model
In December 2014, President Barack Obama announced that nearly $400 million will be allotted to help improve the competitiveness of U.S. businesses and workers by spurring new manufacturing innovations and giving U.S. workers additional opportunities to improve and expand their skill sets for middle-class jobs.
One of those opportunities involves providing $100 million to expand apprenticeships for U.S. workers. The sizable investment is intended to provide middle-class workers access to well-paying jobs. According to a White House statement, 87 percent of apprentices are employed after completing their programs, and the average starting wage for apprenticeship graduates is more than $50,000 annually.
The American Apprenticeships Grants competition will award about 25 grants to partnerships between employers, labor organizations, training providers, community colleges, local and state governments, the workforce system, nonprofits and faith-based organizations that launch apprenticeships in high-growth fields including technology and health care, align apprenticeships to career advancement, and scale apprenticeship models to be effective in all industries and professional levels.
—Sarah Sipek
“In the first year, we had some challenges,” Patta said. “We thought we were offering a nice opportunity, but students weren’t registering it as an opportunity.”
Furthermore, Volkswagen wasn’t exactly casting a wide net. Meacham, a Florida-transplant, heard about the program by accident while researching local colleges after deciding that she would like to go back to school to pursue a different career. Moore already worked in the plant as an unskilled laborer on the assembly line. If it weren’t for his previous affiliation with Volkswagen, he would never have heard about the program, Moore said.
Ideally, each class would have 12 students in the automation mechatronics program and 12 students in the car mechatronics program. In the first year, roughly 40 percent of the class dropped out. There were only 12 graduates in 2013.
The recruiting methods have since evolved. Volkswagen now goes directly to the source, with Gwaltney and Graser having increased their involvement with local high schools.
“We’ve been going to more career fairs,” Graser said. “We invite the schools to come in for open houses. We’ve tried to be more open and in the public eye in order to increase interest. Once we’ve captured the interest of students, we invite them in for information sessions where we take them through a brief overview of what the program is all about.”
In those information sessions, Graser and Gwaltney are sure to hit on two major points: a guaranteed contract and paid training. Upon completing the program, apprentices are given an unlimited job contract, Mette said.
Apprentices are also paid for the semesters they complete hands-on training in the plant. However, the stipend does not extend to the academic semesters.
“That’s one of the things we try to point out to people as they take an information tour through the academy,” Gwaltney said. “We want to make sure they know that there are some dry spells where they are not being paid during those academic semesters. We want to make sure that they have thought about it and made plans for those times because that financial burden that some of these students carry really affects them and their work at school. We want to make sure they understand it upfront.”
For Moore, the possibility of a stable career made a few lean months worth the risk.
“Before I started and quit my job here, I talked with my wife and we budgeted around it so that we would be able to live on one income every other month until I graduated,” Moore said. “We knew that after the three years were up, we were going to have a good life.”
After candidates understand both the sacrifices and benefits of joining the apprenticeship program, they are put through a detailed interview process. While no prior experience in mechanics or electrical engineering is required, candidates take a hands-on test to determine their current skill level, Graser said. The traditional in-person interview probes at whether the program is the correct fit for the applicant. Typically 80 potential students are interviewed for 24 total positions.
Down the Road
Students who enroll in Volkswagen’s apprenticeship program agree to delay full employment for three years while given a bevy of opportunities in return.
Source: Photo courtesy of Volkswagon
Because their certification qualifies them to work at any plant in the world, Volkswagen developed a program called “Wanderjahre” — which means “traveling years” in German — an exchange program that places graduates in the company’s Emden, Germany, plant where the European version of the Passat is manufactured. Patta said participants work overseas for a year and can come back to their position at the Chattanooga plant afterward.
One of the main hurdles American employees have to the apprenticeship model is that it doesn’t result in a bachelor’s degree. In recognition of that fear, Volkswagen now offers students who have completed the apprenticeship the opportunity to pursue a four-year degree while their position at the plant is held for them.
“One of the graduates from our first class is currently pursuing an electrical engineering degree,” Patta said. “It’s one of the most important needs we have for the future. The industry is changing and moving more towards an electrical IT solution. We held his job open because we are interested in getting him back with those skills. We make it flexible.”
In addition to the opportunity to pursue further learning, Volkswagen gives its employees the opportunity to move through the organization in any way they please. Patta himself is a product of this opportunity. He began as an apprentice in Germany 31 years ago, and is now an executive in the human resources department.
“We are very interested in bringing our own people into positions instead of bringing in someone from the outside to fill the higher positions in management,” Patta said. “It’s much nicer if you come up through the program so you are familiar with hands on training before you become a manager.”
Volkswagen has an annual feedback and performance strategy in place that promotes dialogue between superiors and employees. During these sessions, employees have the opportunity to express interest in moving though the company. The onus is on the employee to take the initiative, though.
“It’s a matter of the personal effort you’re willing to put into it,” Patta said. “If you deliver good performance and present yourself in a way that someone becomes aware of you, you will have the opportunity to advance.”
This is a stark difference from the way Americans are currently moving from job to job. According to the U.S. Bureau of Labor Statistics, the typical employee in 2014 had been with their employer for just 4.6 years.
Patta said that the same opportunity for growth is open to all employees who complete the apprenticeship program. All they have to do is express an interest and Volkswagen will help them achieve their career goals.
“It’s a lifelong career,” Patta said. “Every other employee and apprentice will have the same opportunity. It’s not only what the company is doing for you. It’s also what you are willing to do for your future.”
This article originally appeared in Chief Learning Officer's sister publication, Talent Management.