Tyson Foods invests in ESL and GED courses for frontline workers through its Upward Academy.
by Sarah Fister Gale
September 17, 2018
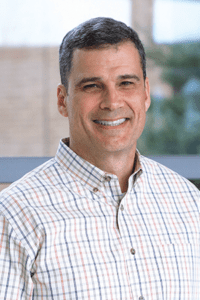
Tyson Foods got its beginnings during the Great Depression when founder John Tyson began delivering chickens from Springdale, Arkansas, to buyers across the Midwest. Nearly 90 years later, Tyson has become the second largest processor of chicken, beef and pork in the world, with more than 100,000 employees across the country and nearly $40 billion in annual revenues — but it still operates that first plant in Springdale, and it’s still deeply invested in the local community and its people.
Springdale is made up largely of immigrants who came to Arkansas in search of a better life, and the company wanted to be sure it was meeting their needs. In 2015, Tyson conducted an employee satisfaction survey of frontline plant workers at Springdale and discovered that many of them were interested in English language learning programs.
In response, the employee social responsibility team rolled out a small pilot program offering English as a second language training at the plant. “We thought 10 or 15 people might show up,” said Kevin Scherer, senior manager of the ESL team. So he was shocked when 128 employees of the 300 total staff attended the first class. “We realized the survey was trying to tell us something important,” he said.
After the first program was launched at the Springdale plant, Scherer’s team got permission to institute it at a larger plant in Arkansas. Again, they were worried nobody would be interested. This time, 250 employees out of 1,100 signed up. “It wasn’t a fluke,” Scherer said. “The rest is history.”
Government-Funded Training
While English language skills are obviously important for plant communication, Scherer’s team wanted Upward Academy, as the employee education program came to be known, to focus on more than just workplace productivity. “We wanted to help them with their lives outside the plant,” he said. So they decided they needed a learning program that would help employees navigate everything from renting an apartment and scheduling doctor’s appointments to figuring out transportation and talking to their kids’ teachers.
When Scherer presented the idea to the executive team, they were immediately on board. “Community is a big part of what Tyson is all about,” Scherer said. They also suspected that helping employees navigate challenges outside the plant would result in a more productive, loyal and engaged workforce. “Stable team members drive more stable workforce metrics,” he said.
Rather than attempting to build the program in-house, Scherer’s team began looking for community partners with expertise in ESL and related training. They eventually partnered with the Ozark Literacy Council, a local nonprofit that already offered ESL and citizenship classes. “We were excited to help people gain literacy in the workplace,” said Patty Sullivan, executive director of OLC.
Tyson and OLC were also able to tap funding from the Workforce Innovation and Opportunities Act to cover most of the costs. WIOA is federal workforce development legislation designed to promote adult basic education, which requires organizations like OLC to partner with local businesses to provide training. However, it can be hard for the nonprofit to connect with corporate partners. “When we came knocking, it was a great match,” Scherer said.
Break Room or Classroom
In the week leading up to the first class, representatives from the council came to the plant before and after every shift to talk about the course and to help people sign up. The representatives spoke employees’ native language and brought coffee and donuts, said Emily Hackerson, program consultant for Upward Academy. “Having someone who could speak to them in their native language was important,” she said.
When an employee showed interest, the reps walked them through the application and gave them a brief test to assess their needs. “Having the representatives there helped them establish trust, and it showed them that this wasn’t just some check-the-box initiative,” Hackerson said. “We think it is one of the reasons Upward Academy has been so successful.”
Upward Academy classes are held at the plant before and after shifts, with instructors coming as early as 4:30 a.m. for some classes and returning late in the evening for others. This allows participants to have the most access possible without missing a beat at work, said Donna Davis, program consultant for Upward Academy. “They also feel safer learning here with their peers.”
The plants weren’t designed for daily classes, so instructors have had to carve out learning spaces in breakrooms, meeting rooms and anywhere else they can find free space and chairs. “At first we thought it would be distracting, but it actually turned into an opportunity,” Sullivan said. When other employees are able to see the classes taking place, it peaks their interest. “They see how much everyone is talking and laughing and they want to get involved,” she said. That has helped keep enrollment high and has become a powerful grassroots tool to market the program.
The instructors interact with staff outside of class to ensure their content addresses the needs of workers inside and outside the facility. Sullivan noted they keep a running list of plant-specific vocabulary words, including pallet, forklift and HVAC, which they incorporate into the lessons and flash cards. “We are delighted to adapt the classes for [the] plant environment,” she said.
Big Benefits
Today, Upward Academy has more than 1,000 participants in 26 locations across four states. Tyson’s team has partnered with eight different literacy councils and nonprofit groups to provide the training, which now includes beginner and advanced ESL classes, citizenship training, financial literacy classes and GED programs for employees who want to get their high school diplomas. Tyson also began offering health care and back-to-school events for Upward Academy participants’ children in 2017 to expand the program’s reach.
Last year alone, the program delivered more than 40,000 hours of training. In 2018, 15 new locations will be added, and over the next five years the company plans to provide the entire Tyson plant-footprint with Upward Academy classes.
“One thing that makes this program unique is that it is ongoing,” Hackerson noted. “Students set their own education goals and they participate until they feel ready to move on or to set new goals.”
Twila Corter is one of the many Tyson employees who has benefited from Upward Academy. Corter has worked at Tyson’s Springdale plant since 2000 doing inventory and providing maintenance support. Last October, she saw a sign for a GED course in the plant break room and was intrigued. Corter quit school in 10th grade, but she saw the classes as an opportunity to go back. “I wanted to better myself for my job, and I wanted my kids to be proud of me,” she said. Corter also teaches a teen Sunday school program, where one of her students dropped out of high school. “When I have my certificate I want to show him that if I can do it at my age, he can do it at his,” she said.
Within a day of seeing the flyer, Corter was participating in her first GED classes. She now studies history, U.S. government, economics and other courses two to four days a week with six other employees, and she hopes to be ready to take her GED soon. “It has been a long time since I was in school, but if I have problems my teacher helps me,” she said. The classes have already helped her improve her performance at work, and she said she is grateful to Tyson for making the program available. “A lot of companies probably wouldn’t do this, but I think it’s wonderful,” she said. “It shows they care enough about their employees to actually give them the tools to make themselves better.”
The primary goal was to improve employees’ quality of life, though the program is also having a positive impact on the business. After the first six months, Tyson found retention among Upward Academy students was higher than the rest of the workforce, and more than 62 percent of those enrolled recorded an educational gain from October to December 2017.
The training is also helping to create a more engaged and satisfied workforce, Scherer said. In a survey of students at 16 plants, 86 percent say they have improved their communication skills at work and in the community, 85 percent say they are happier in the workplace and 77 percent feel more loyal to the company. “Workforce metrics are very important to Tyson, and these numbers demonstrate a positive ROI for this program,” Scherer said. “It shows this isn’t just the right thing to do, it’s also good for the business.”
Sarah Fister Gale is a writer based in Chicago. She can be reached at editor@CLOmedia.com.